The Essential Guide to Plastic Injection Molding Manufacturers
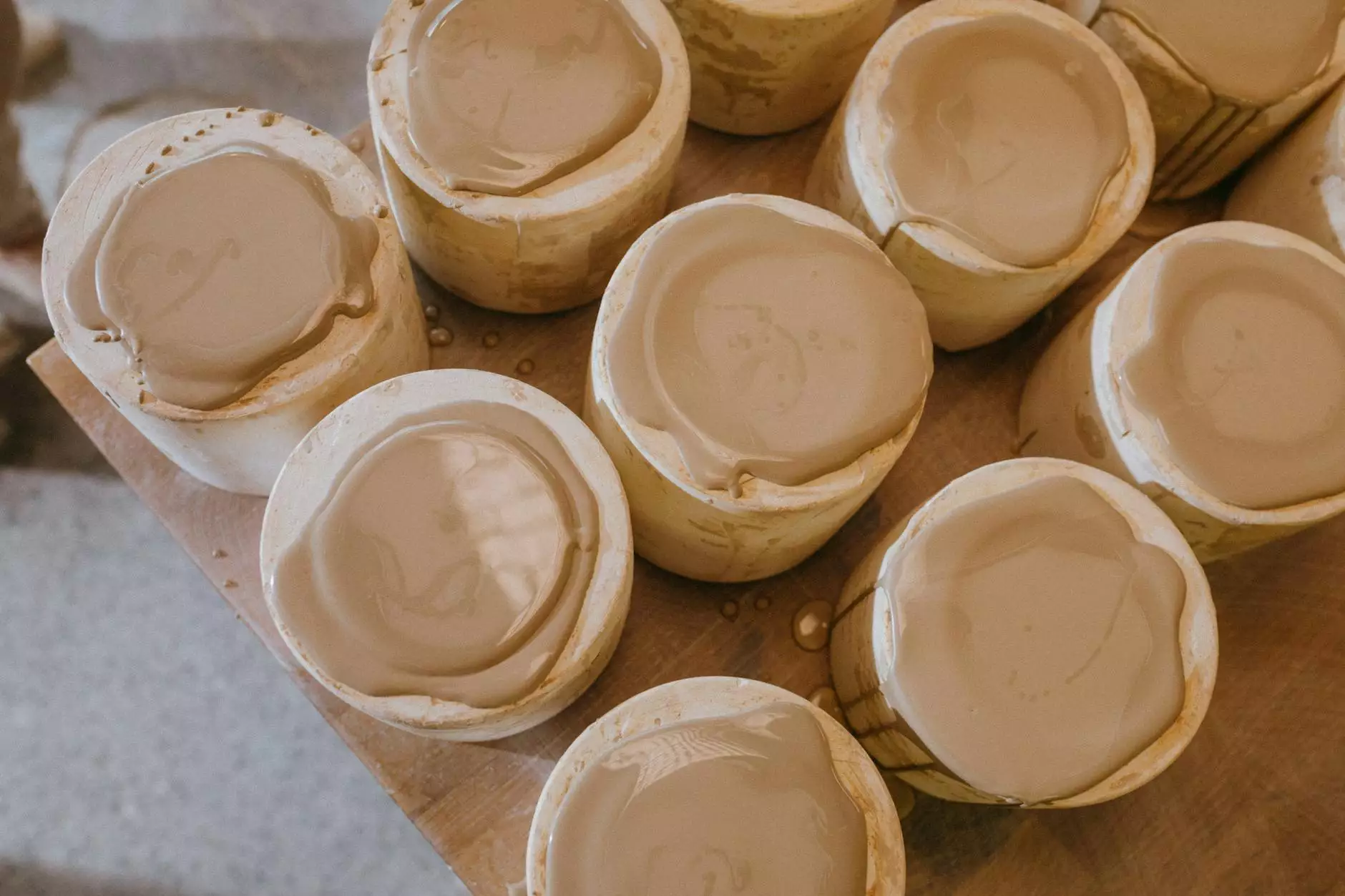
In today's rapidly evolving manufacturing landscape, the role of plastic injection molding manufacturers cannot be overstated. This article will delve deep into the intricacies of the plastic injection molding process, its benefits, and the critical role manufacturers play in ensuring efficiency and quality across various industries.
Understanding Plastic Injection Molding
Plastic injection molding is a manufacturing process used to create parts by injecting molten material into a mold. It is one of the most common and efficient methods for producing plastic products. The process entails several key stages, including:
- Material Preparation: The selected plastic particles are fed into a hopper and then heated to melt them.
- Injection: The melted plastic is injected into a mold under high pressure.
- Cooling: The material is allowed to cool and solidify in the mold.
- Ejection: The solidified part is ejected from the mold for further finishing and assembly.
Key Advantages of Plastic Injection Molding
Plastic injection molding offers numerous advantages that make it the preferred manufacturing method for many companies:
- High Efficiency: Once the mold is made, parts can be produced quickly, significantly reducing production time.
- Complex Shapes: Injection molding allows for intricate designs that would be difficult to obtain using other manufacturing techniques.
- Material Versatility: A wide variety of plastics can be used, including thermoplastics, thermosetting plastics, and more.
- Cost-Effectiveness: While the initial mold creation can be expensive, the low cost per unit during mass production balances it out.
- Reduced Waste: The process generates minimal scrap material compared to other manufacturing methods.
What to Consider When Choosing a Plastic Injection Molding Manufacturer
When selecting the right plastic injection molding manufacturer, several key factors should be considered to ensure a successful partnership:
1. Experience and Expertise
Choose a manufacturer with extensive experience in the industry. Their knowledge can lead to more efficient production processes and better quality products.
2. Technology and Equipment
The latest technology can improve production efficiency, reduce cycle times, and enhance product quality. Ensure the manufacturer invests in state-of-the-art molding machines and technology.
3. Quality Assurance
Look for manufacturers that adhere to strict quality control processes. Certifications such as ISO 9001 can be indicative of quality standards.
4. Material Selection
Ensure that the manufacturer can provide a wide range of materials suitable for your specific application.
5. Customer Support
Strong customer support can ensure seamless communication and address any issues that may arise during production.
Applications of Plastic Injection Molding
Plastic injection molding is employed across various industries. Here are some key applications:
Automotive Industry
The automotive sector utilizes plastic injection molded parts for various components, including dashboards, panels, and bumpers, providing lightweight and durable alternatives to metal.
Medical Devices
In the medical field, precision and sanitation are crucial. Plastic injection molding allows for the production of components used in medical devices, ensuring compliance with strict regulatory standards.
Consumer Goods
From kitchen utensils to toys, the consumer goods industry relies heavily on plastic injection molding for cost-effective production of a variety of everyday items.
Electronics
Plastic housings and connectors in electronics thrive on the accuracy and efficiency that injection molding provides, making it indispensable in the tech sector.
Environmental Considerations in Plastic Injection Molding
As industries become more aware of their environmental impact, plastic injection molding manufacturers are also evolving. Here are some ways they are addressing sustainability:
1. Use of Recyclable Materials
Many manufacturers now offer products made from recyclable plastics, reducing waste in landfills and promoting a circular economy.
2. Energy Efficiency
Advancements in machine technology have led to more energy-efficient operations, helping manufacturers reduce their carbon footprint.
3. Waste Reduction Techniques
Implementing waste reduction techniques during the molding process can further minimize environmental impacts.
Future Trends in Plastic Injection Molding
As technology and market demands evolve, the plastic injection molding industry is experiencing several noteworthy trends:
1. Automation and Robotics
The rise of automation in manufacturing processes enhances efficiency and reduces labor costs. Robotics are increasingly used for tasks such as loading and unloading molds.
2. 3D Printing Integration
3D printing technologies are complementing injection molding processes, particularly in creating prototypes and complex mold designs more rapidly and affordably.
3. Smart Manufacturing
Internet of Things (IoT) technologies are being integrated, providing real-time data on machine performance and enabling predictive maintenance. This can significantly improve operational efficiency.
4. Focus on Customization
As consumer needs grow more specific, manufacturers are increasingly offering custom solutions, allowing businesses to tailor products to their unique specifications.
Conclusion
In summary, plastic injection molding manufacturers play a pivotal role in modern manufacturing, serving various industries with innovative and efficient solutions. By understanding their processes, benefits, and future trends, businesses can make informed decisions when selecting a partner for their production needs. Investing in a skilled manufacturer not only enhances product quality but also contributes to long-term sustainability and success in the competitive marketplace.
For more information or to discover how DeepMould can assist you with your plastic injection molding needs, please visit deepmould.net