The World of Plastic Molding Factories: Transforming Ideas into Reality
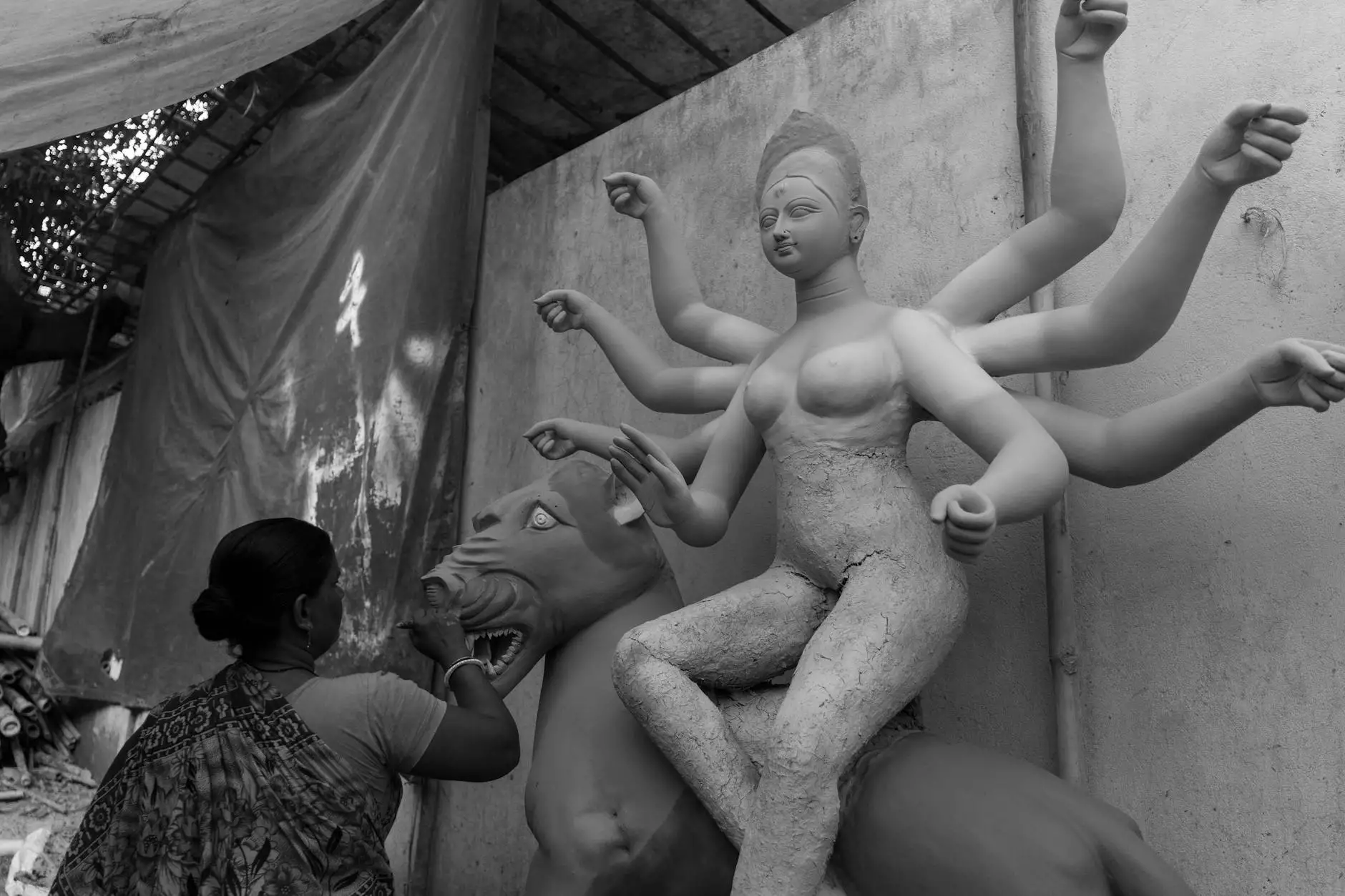
The manufacturing landscape is rapidly evolving, with innovations and technologies shaping the way we approach production. At the heart of this transformation lies the plastic molding factory, a powerhouse that plays a vital role in turning concepts into tangible products. In this article, we delve into the intricacies of plastic molding, its significance in various industries, and why investing in a quality plastic molding factory is essential for businesses today.
Understanding Plastic Molding
Plastic molding is a manufacturing process that involves shaping plastic materials into desired forms. This process is fundamental to producing a vast array of products, from household items to complex components used in aerospace and automotive industries. The core principle of plastic molding is to heat plastic to its melting point, then inject it into a mold where it cools and solidifies into the desired shape.
The Process of Plastic Molding
The process in a plastic molding factory can be broken down into several key stages:
- Material Selection: Choosing the right type of plastic is crucial. Different plastics offer varying degrees of strength, flexibility, and resistance to heat or chemicals.
- Design and Prototyping: Before mass production, a prototype is often created to ensure the design meets specifications. Advanced CAD (Computer-Aided Design) software is frequently used for precision.
- Mold Creation: Molds are designed and fabricated, usually from metal. This step is critical as the mold's quality will affect the final product's quality.
- Injection Molding: The melted plastic is injected into the mold under high pressure. This process must be closely monitored to ensure consistency and avoid defects.
- Cooling and Ejection: Once the plastic has cooled and solidified, the mold is opened, and the product is ejected.
- Finishing Touches: Additional processes such as trimming, polishing, and assembling may follow to enhance the product's usability and aesthetics.
Types of Plastic Molding Processes
Within the realm of plastic molding, there are several processes utilized by factories, each with its unique advantages:
- Injection Molding: This is the most common method in plastic molding factories, known for its efficiency and ability to produce high volumes at low costs.
- Blow Molding: Used primarily for making hollow objects like bottles, this technique involves inflating a hot plastic tube into a mold.
- Rotational Molding: This process is ideal for producing large, hollow items and involves rotating a mold to distribute heated plastic evenly.
- 3D Printing: While not traditionally associated with molding, this innovation is becoming a fast-growing method for creating prototypes and small production runs.
The Advantages of Choosing a Reliable Plastic Molding Factory
Partnering with a reputable plastic molding factory can bring numerous benefits to businesses including:
1. Cost Efficiency: High-volume production significantly reduces the cost per unit, making it a budget-friendly option for manufacturers.
2. Versatility: A wide range of materials can be processed, allowing manufacturers to choose the best fit for their product requirements.
3. Precision and Quality: Advanced machinery and skilled technicians ensure high-quality and precise dimensions, reducing waste and maximizing efficiency.
4. Quick Turnaround: A well-equipped plastic molding factory can produce thousands of units in a short time frame, which is crucial in today’s fast-paced market.
Applications of Plastic Molding
The applications for molded plastic products are vast and diverse. Here are some key industries that benefit from plastic molding:
1. Automotive Industry
Automotive manufacturers utilize plastic molded components for everything from dashboard parts to bumpers. The lightweight nature of plastics also helps improve fuel efficiency by reducing vehicle weight.
2. Consumer Goods
Household products such as containers, toys, and kitchenware are often created through plastic molding. The durability and versatile design options help brands deliver innovative products that meet consumer needs.
3. Medical Field
Medical devices and instruments require high precision and hygiene standards. Plastic molding allows for the production of disposable items like syringes and surgical tools that are both safe and effective.
4. Electronics
In the electronics sector, molded plastic parts are essential for enclosures, connectors, and insulators. The ability to integrate design and functionality makes molding a preferred method for creating complex electronic components.
Challenges Faced by Plastic Molding Factories
While there are numerous advantages to plastic molding, factories also face certain challenges that must be overcome:
- Material Costs: Fluctuations in the prices of raw materials can affect production budgets.
- Environmental Concerns: With growing awareness of environmental issues, plastic molding factories are challenged to implement sustainable practices and explore biodegradable materials.
- Technological Upgrades: Staying competitive requires continuous investment in the latest equipment and technology.
Future Trends in Plastic Molding
The future of plastic molding is poised for exciting developments. Here are a few trends to watch:
- Sustainability: Increasing pressure to reduce plastic waste is leading to innovations in recyclable and biodegradable plastics.
- Smart Molding Technologies: The integration of IoT (Internet of Things) technologies allows for real-time monitoring and adjustments during the molding process.
- Advanced Robotics: Automation is set to enhance productivity and minimize human error in factories.
Choosing the Right Plastic Molding Partner
When selecting a plastic molding factory, companies must consider several factors to ensure they are making the right decision:
- Experience and Reputation: Look for a manufacturer with a solid track record and positive client testimonials.
- Production Capabilities: Ensure that the factory has the necessary equipment and expertise to handle your product requirements.
- Quality Assurance Processes: A reliable factory will have rigorous quality checks to guarantee product consistency.
- Communication and Support: Choose a partner that maintains open lines of communication throughout the production process.
Conclusion
In conclusion, "plastic molding factory" plays an indispensable role in the modern manufacturing landscape. As industries continue to evolve and adapt, the demand for innovative solutions in production processes will grow. By understanding the intricacies of plastic molding, its significant benefits, and its future trends, businesses can make informed decisions about their manufacturing needs.
Whether it be in the automotive, consumer goods, medical, or electronics sectors, a quality plastic molding factory offers the technology, expertise, and support essential for success. As we move further into the 21st century, the innovations within this field will undoubtedly shape the future of manufacturing, presenting new opportunities and challenges for businesses worldwide.
For more information on plastic molding manufacturing and opportunities to partner with a leading factory, visit deepmould.net.