Understanding the Importance of Pressure Die Casting in Metal Fabrication
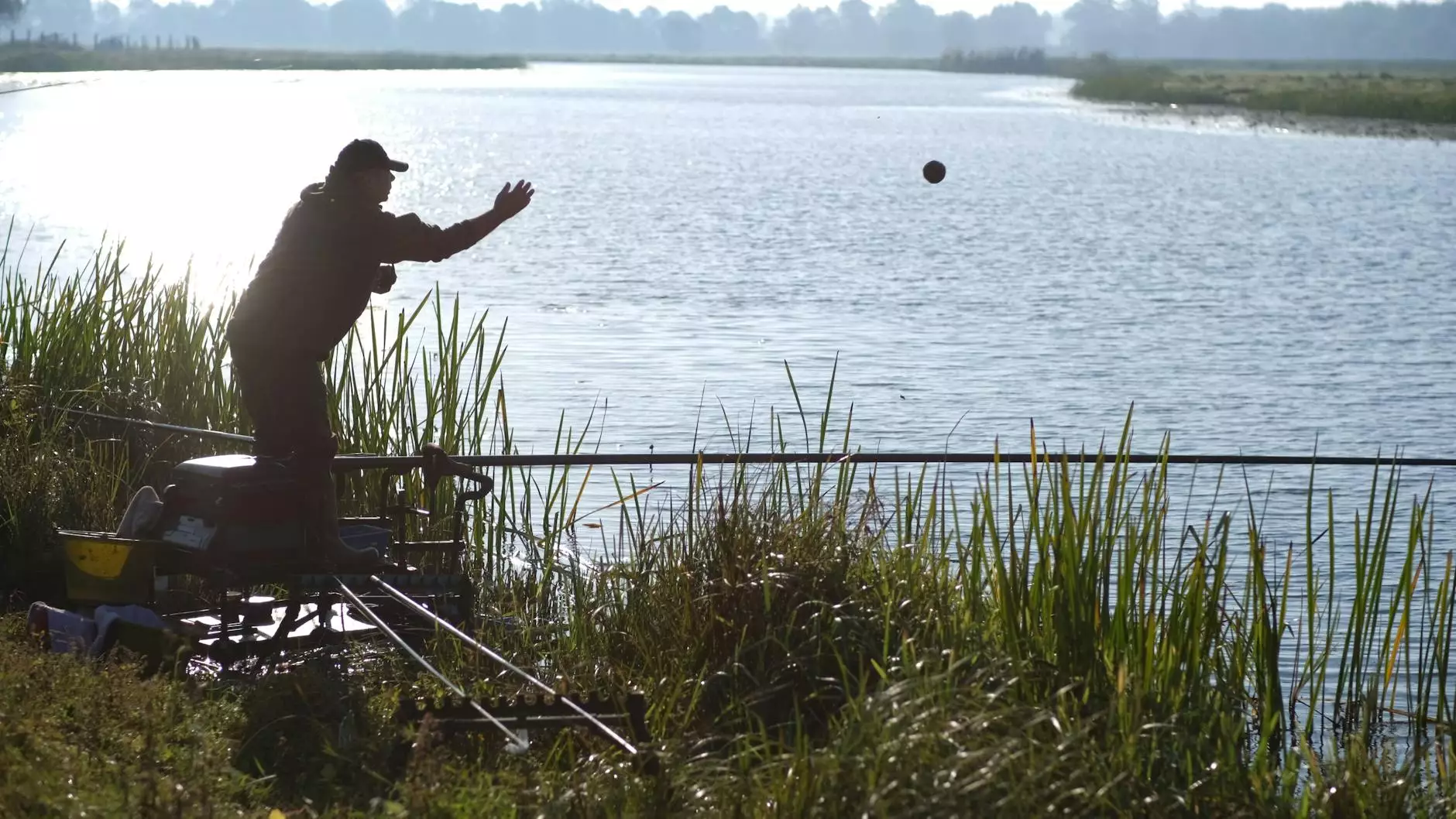
Pressure die casting has emerged as a cornerstone of modern manufacturing, particularly within the realm of metal fabrication. It involves forcing molten metal into a mold under pressure, which allows for the creation of complex shapes with exceptional precision. In this article, we will delve into the intricacies of pressure die casting and highlight why partnering with a specialized pressure die casting factory like deepmould.net can significantly enhance your product development and manufacturing processes.
What is Pressure Die Casting?
Pressure die casting is a manufacturing process that utilizes high pressure to inject molten metal into a mold. This innovative technique is designed to produce parts that have high dimensional accuracy and a fine surface finish, making it a preferred choice in industries ranging from automotive to electronics.
Advantages of Using a Pressure Die Casting Factory
Utilizing a specialized pressure die casting factory such as Deep Mould offers a myriad of benefits:
- High Precision and Accuracy: The pressure die casting process ensures that the finished components match the exact specifications required.
- Cost Efficiency: Mass production allows for the reduction of manufacturing costs while maintaining quality.
- Material Versatility: A variety of metals, including aluminum, zinc, and magnesium, can be used to create products suited for different applications.
- Rapid Production Times: The process's efficiency enables quicker turnaround times, which is crucial in today’s fast-paced market.
The Process of Pressure Die Casting
The pressure die casting process consists of several key steps:
- Mold Creation: The creation of durable molds from hard steel to withstand the high-pressure injection process.
- Melting the Metal: The metal is melted in a furnace and prepared for injection.
- Injection: Molten metal is injected into the mold at high pressure, filling the cavity completely.
- Cooling and Solidification: Once the mold is filled, the molten metal begins to cool and solidify, taking the shape of the mold.
- Removal: After the metal has hardened, the mold is opened and the finished component is ejected.
- Trimming: Any excess material or flash is trimmed away to produce the final product.
Applications of Pressure Die Casting
Pressure die casting is utilized across a broad spectrum of industries, including but not limited to:
- Automotive: Used for engine components, transmission cases, and various structural parts.
- Aerospace: Precision components that require lightweight yet strong materials.
- Electronics: Enclosures and housings for various electronic devices.
- Consumer Products: Manufacturing parts for appliances, tools, and furniture.
Key Considerations When Choosing a Pressure Die Casting Factory
Partnering with a pressure die casting factory is a significant decision for your manufacturing needs. Here are some essential factors to consider:
- Experience and Expertise: Look for a factory with a proven track record in precision die casting and familiarity with your specific industry.
- Quality Control Processes: Ensure that the factory adheres to strict quality control measures to maintain product integrity.
- Technology and Equipment: The factory should use advanced die casting machines and technology to enhance production quality.
- Customer Support: Strong communication and support from the factory can help resolve issues quickly and efficiently.
Future Trends in Pressure Die Casting
The future of pressure die casting is bright, with ongoing advancements that are shaping the industry:
- Automation: Increasing automation in manufacturing, such as robotic handling of materials, enhances efficiency.
- Sustainability: Innovations in eco-friendly practices and recycling of materials are becoming more prevalent, reducing the environmental impact.
- Advanced Alloys: Development of new metal alloys capable of withstanding higher stress and providing even better performance.
- Integration with 3D Printing: Combining traditional die casting with 3D printing technologies is opening up new possibilities for complex part shapes.
Conclusion: The Role of Pressure Die Casting in Modern Manufacturing
The role of a pressure die casting factory in the manufacturing landscape is undeniable. With the ability to produce high-quality, intricate components at scale, businesses can meet the demands of a competitive market. By choosing a reliable partner like deepmould.net, companies can ensure they are at the forefront of innovation and quality in metal fabrication.
As we continue to embrace the technology and advantages offered by pressure die casting, it will undoubtedly remain a vital component in driving industrial efficiency and excellence. Explore your options today and see how pressure die casting can transform your manufacturing capabilities!